In today’s dynamic industrial world, managing production processes requires advanced tools and technologies that support efficiency, quality and safety. Plus Workflow is a solution that adapts to the needs of manufacturing departments, automating key aspects of managing, scheduling and controlling production processes. Our solutions not only provide precise planning and quality control, but also improve maintenance and documentation management, supporting your company in achieving the highest production standards.
Solutions for the manufacturing industry
Thanks to the Plus Workflow platform, you can gain full control over every stage of production, from inventory management to efficiency monitoring, allowing you to optimize operations and increase productivity. Explore the applications available on the Plus Workflow platform dedicated to manufacturing
How can we help you?
The Plus Workflow platform facilitates, among other things, the acceptance of chemicals and the change of production technology, ensuring that all changes made are in accordance with industry and legal requirements and standards. Automating the processes of acceptance of technological tests and product specifications positively influences their duration and increases their precision. Our tools also support the distribution of technical documentation, ensuring consistency and compliance throughout the production cycle.
We optimize the work of manufacturing companies in the areas of:
- Substance documentation management
- Testing and technological changes
- Workflow of technical documentation
- Formulation monitoring
- Compliance with standards and legal regulations
- Coordination of internal audits
- Quality management
- Production cost control
Implementation of the Plus Workflow system enables manufacturing companies to quickly and efficiently implement various types of product and technological innovations, which increases their competitiveness and ensures a stable position in the market. In addition, improving control over production processes positively influences the quality of products, as well as better use of raw materials. Thanks to the optimal management of resources, the enterprise eliminates not only unnecessary financial expenses, but also minimizes the risk of downtime and operational errors.
Implementation example: Supporting production work at Nord Glass
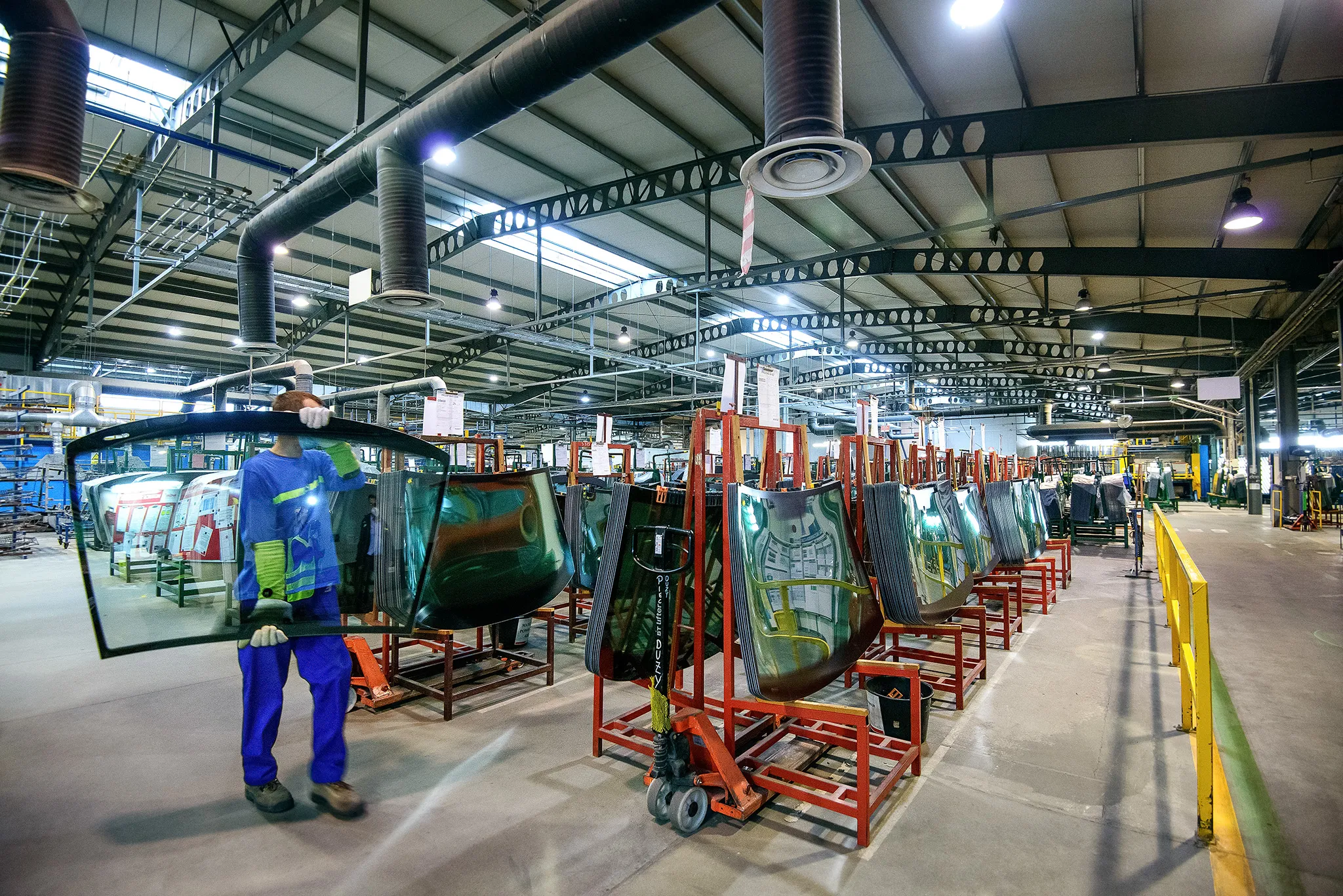
NordGlass is a leading manufacturer of automotive windshields, specializing in providing high-quality products for the automotive industry. The company’s products are available in international markets, and its commitment to quality and precision in production has won recognition among numerous customers and business partners.
The cooperation with NordGlass has included, among others, the process of external and internal audits, enabling accurate assessment and optimization of quality procedures, the process of supervision of control and measurement equipment, allowing high precision of production work, the process of supervision of patterns, facilitating the maintenance of accepted standards, or the process of corrective and preventive actions, which improves the identification and analysis of problems and their causes, as well as the implementation of effective solutions to eliminate defects.
As a result, the company has not only gained better control and compliance with production standards, which translated into an increase in the quality of manufactured products, but also significantly reduced downtime.
The most common appilcations chosen by customers:
- Acceptance of a chemical substance
- Change of production technology
- Acceptance of technological tests
- Acceptance of product specifications
- Acceptance of packaging designs
- Acceptance and distribution of technical documentation
- Acceptance and review of recipes
- Registration of equipment
- Reporting of breakdowns
- Scheduling overhaul and maintenance of equipment
- Plus Label Printer module
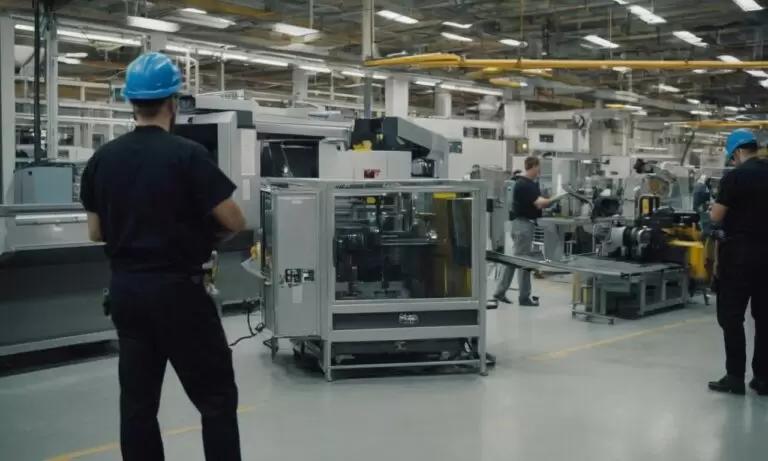